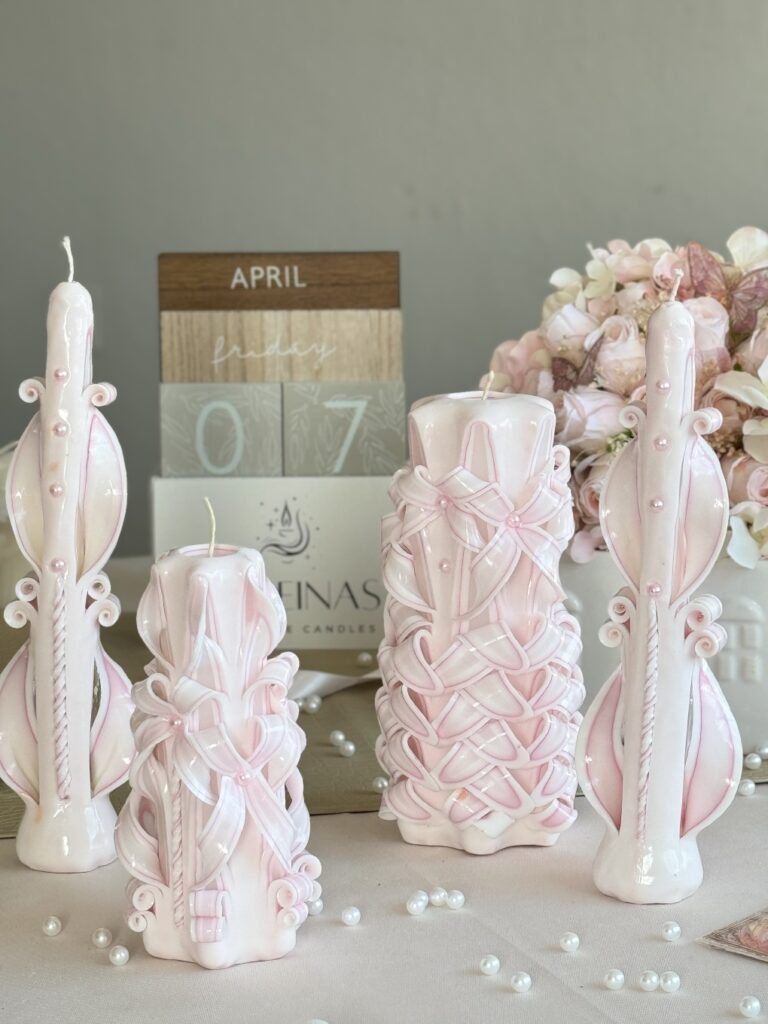
Crafting Unique Handcrafted Carved Candles at Home
At Luminus, we believe that candle-making is a wonderful way to express creativity and add a personal touch to your home interior decor. In this blog, we’d like to share a summary of the years of experience we’ve gained since we first started learning the art of handmade carved candles at a workshop in Dublin, Ireland, in 2019. Over the years, we’ve developed our skills and gathered extensive knowledge in this unique craft. Today, we’re excited to guide you through the process of making carved candles at home, step by step, so you can create beautiful, one-of-a-kind candles that reflect your personal style.
The History of Carved Candles
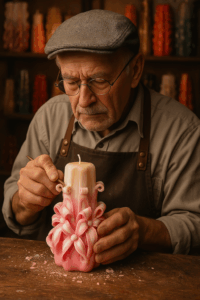
The art of candle carving began in the 16th century, primarily in Europe, where it was practiced by skilled artisans for the wealthy elite. These hand-carved candles were considered luxury items and were often used in royal ceremonies and important religious rituals, symbolizing status and refinement.
With the rise of industrial production, the popularity of intricately carved candles declined in favor of cheaper, mass-produced alternatives. However, the craft experienced a revival in the late 20th century as artists began restoring traditional methods. Today, carved candles are once again cherished for their beauty and uniqueness, serving as personalized gifts and elegant decorative pieces that bring an artistic touch to any space.
Step-by-Step Guide on How to Make Carved Candles at Home
Creating handmade carved candles at home is a fun and rewarding experience. Here’s a detailed step-by-step guide on how to make handmade carved candles at home, ensuring that you create candles that are both beautiful and unique.
Materials and Tools Needed to Make Carved Candles at Home
Before you begin crafting your beautiful, decorative candles, you’ll need the right tools and materials. Here’s a list of what you’ll need:
- Paraffin Wax: The most common type of wax used in candle making, known for its durability and ease of handling.
- Candle Dye: To add vibrant colors to your candles.
- Carving Tools: Small, precise tools such ascarving knives to create intricate designs.
- Candle Molds: Molds to form the basic shape of your candles.
- Wick: A wick to light your candles once they are finished.Wax
- Melter: A tool to melt your wax evenly and maintain the right temperature.
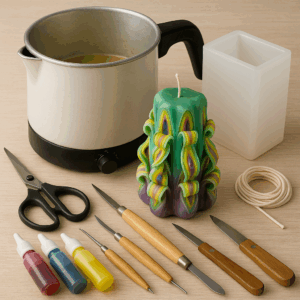
Step1:Preparing the Wax
- Use a wax melter to safely melt paraffin wax.
- Maintain a consistent temperature of 60°C (140°F) to avoid overheating, which can affect texture and color.
- Once fully melted, add candle dye to achieve your desired color.
- If using multiple colors, divide the melted wax into separate portions.
- Add a different dye to each portion to create layered, multi-colored candles.
Step 2: Pouring the Wax into Molds
- Once your wax is ready, you can start pouring it into your candle molds.
- Make sure the wick is centered properly before you start pouring.
- Allow the wax to set and harden completely. This will form the basic structure of your big candles.
- Once hardened, you can proceed to add additional layers and textures to make the candle carvable.
Step 3: Dipping the Candle in Hot Wax
- Now comes the fun part — creating the intricate layers that make carved candles so special.
- Once the wax in the mold has hardened, carefully dip the candle into hot wax at a temperature of 60°C (140°F) several times.
- Each dip adds a new layer of wax, and you can choose different colors for each layer.
- Between each dip, the candle should be quickly dipped into cold water for about 3 seconds. This helps the wax layer set slightly before the next dip.
- After the water dip, gently wipe the candle with a soft cloth or tissue to remove any excess moisture.
- Repeat the dipping process until the candle reaches the desired size and number of layers.
- For the final dip, do not submerge the candle in water — instead, let it cool naturally at room temperature.
- This preserves the glossy finish of the outer layer and prepares the candle for carving.
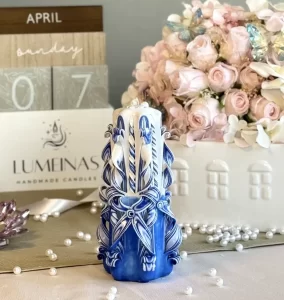
Step 4: Carving the Candle
- Use your carving tools to create detailed patterns, swirls, or any design that speaks to your artistic side.
- With each cut and carve, you’ll reveal the layers underneath, creating stunning visual effects.
- Don’t be afraid to experiment with different designs to make your handmade carved candles truly one-of-a-kind.
Step 5: Final Touches and Decoration
- Smooth out any rough edges using a warm tool or polish the surface for a sleek, professional finish.
- Add decorative elements like glitter, beads, or even a touch of fragrance to enhance your design.
- These additions bring a personal and creative touch to your handmade carved candle.
- Final details help turn your candle into an unforgettable gift that stands out.
Conclusion
The process of making carved candles may seem somewhat complex, as it requires effort and precision, and producing them in large quantities is not easy. However, it is a truly enjoyable and artistic experience that calls for skilled hands and a refined sense of aesthetics. This type of craftsmanship has become rare today and is considered part of a heritage that deserves appreciation and preservation. These candles are not just decorative items; they are works of art that express passion and creativity.
At Luminus, we are dedicated to reviving this beautiful art after noticing a growing interest from a distinguished clientele who truly value rare craftsmanship and seek elegance and uniqueness. Through our work, we aim to preserve this traditional art and highlight its beauty in every piece we create.